A Potential Path for Savings & Sustainability
Powder coatings in EV production promise potential boosts to the sustainability and resilience of electric vehicles. Parts with short life cycles last longer, and manufacturers waste less money on unnecessary repairs, maintenance and production. We’ll address two questions: How could switching from paint to powder coatings alter EV adoption? Why are they not yet the industry standard?
Durability and Resistance
Paint corrodes and flakes, proving environmental stressors weaken its adhesion. The sun’s UV rays cause peeling and cracking, and temperature variations reduce performance efficacy on parts like tires.
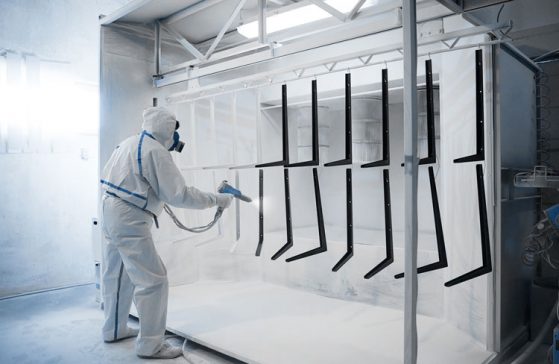
Powder coatings provide EVs with increased corrosion resistance and defense against volatile climates. Multiple layers add to the car’s strength, mainly when applied thinly. The innermost coat may prevent battery degradation, while manufacturers design subsequent layers to ensure electromagnetic stability and weatherability.
This makes everything from circuits to wires last longer. Excessive under-the-hood preventive maintenance decreases, and long-term wear from moisture and chemicals becomes less impactful. Powder coatings also offer protection from external elements. Stones, debris and other objects cause less damage because of increased impact resistance.
One challenge facing powder coating adoption is its limited range of suitable substrate materials. Potentially more durable options could enter the market, but the curing process means everything must withstand specific temperatures. Anything that could liquefy, burn or warp in these conditions is not an option, which omits some fiberboard densities and several plastics.
Sustainability Benefits
EVs have a contradictory reputation regarding their carbon footprint. Mining lithium for batteries tarnishes its value, while leveraging renewable energy and vehicle-to-grid applications provides a more promising perspective. Powder coatings magnify eco-friendly benefits in several ways, which levels climate discourse.
Paints contain volatile organic compounds and metals that easily spread and pollute wildlife and habitats. Air and waterways suffer and trophic transfer occurs, impacting human health. No solvents are present in powder coatings, rendering their VOC impact almost zero.
They also emit little waste compared to paint. Powder coatings’ electrostatic nature uses 95% less waste than spray paints. Manufacturers can easily capture and recycle flyaway product for reuse, whereas paint can run off or seemingly disappear into the air. It makes work environments less hazardous for workforces and biodiversity. The waste benefits compound as the EV requires fewer recoats during its life span.
Applying powder to an EV and its parts demands less energy and lower temperatures for curing than paint. Powder coatings cure in cooler environments, lessening greenhouse gas emissions. Manufacturers can justify a renewable transition when expenditure eases.
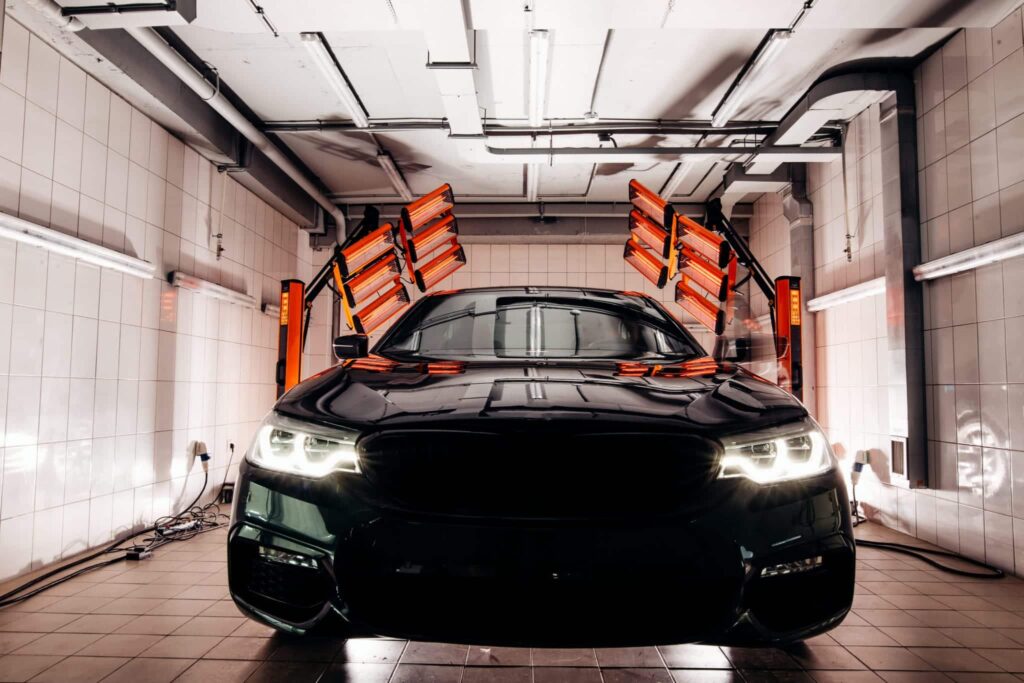
Cost-Effectiveness
Powder coatings help ESG and vehicle quality, but how does it affect bottom lines? Acknowledging high upfront costs is crucial for companies performing cost-benefit analyses. Expenses vary depending on if a business hand applies, uses automation or employs large conveyors. Prices increase for the latter two, but foundational expenses include:
- Licenses, permits and other legal certificates and fees
- Recovery or nonrecovery coating booths and compliant shielding
- Staff training
- Dip tanks and other metal washing peripherals
- Coating guns and other application tools
- Powder coatings and varieties
- Work surface treatment materials, like paint-removal products and sandblast pots
- Infrared or convection ovens
Large outfits should expect to spend hundreds of thousands, though heightened longevity may equate to lower maintenance and parts costs over time. Labor expenses drop while productivity skyrockets because fewer workers are devoted to repairs and more focus is on production. Manufacturing cycles shorten because of faster application and curing, demonstrating how they save money during every step.
Refined operations yield fewer rejects and defective EVs. This improves customer satisfaction and deters unplanned stops, curtailment and other money-wasting incidents.
The eco-conscious benefits also translate to financial savings. Lower energy bills and maximized material utilization might seem inconsequential in the short term, but they add up. Climate-related legislation is also intensifying the strictness of environmental compliance, and powder coatings might be quintessential for keeping VOC and air pollutant numbers at acceptable levels. This eliminates unnecessary fees and penalties manufacturers pay for failing to adhere.
Design Flexibility
Powder coatings enable manufacturers to make more creative aesthetic and practical design choices. Custom options and color changes lengthen lead times even longer than paint. Even though powder dry times are shorter, the process is more involved, especially with color matching and curing. The powder’s lightness gives it more versatility than paint. For example, EV weight is a prominent megative attribute, but thin film options lower the impact compared to conventional paints that would add weight.
However, producing these thin coatings is another reason powders are not as commonplace as paint. The locus of materials is in China, which struggles to develop thin powder coatings quickly because urbanization, appliances and infrastructure are taking precedence over automobile advancements. A lack of raw material source diversity places many stopgaps in expedited production.
Though substrate materials are limited, powder’s compatibility with market-standard substrates gives them relative adaptability. Curated powder coating formulations meld well with everything from plastic to aluminum. It makes up for the shortcomings of certain parts, like supplementing the security of gaskets and the hydrophobic qualities of crevices.
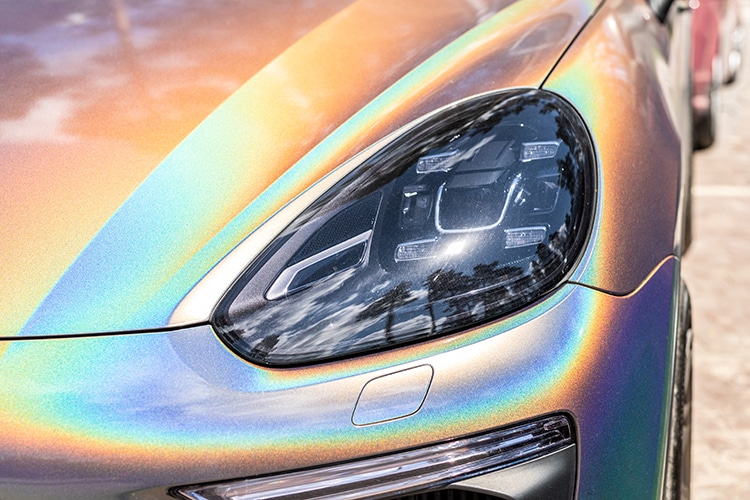
Makers feel encouraged to forge parts from whatever materials suit the application best or with what is available in the supply chain. With selective application, each EV facet can have improved surface quality while glowing in customized, detailed graphics.
Leveraging Powder Coatings for Long-Term Advantages
Some roadblocks prevent EVs from becoming the true sustainability beacon they need to be for an automotive revolution. No single solution exists to dissolve all manufacturing challenges, but powder coatings alleviate the burdens of many. They compound the eco-friendliness of EVs while making them less expensive and accessible to produce.
Manufacturers must consider how these pros compound each other to provide competitive advantages and corporate resilience while achieving environmental objectives.
2 thoughts on “EV Manufacturers Should Consider the Benefits of Powder Coatings”