Making Sure Batteries Hold Up Longer
Car battery corrosion occurs when the sulfuric acid inside the battery releases hydrogen gas. That process creates a corrosive environment when the gases react to the ambient atmosphere. Exposure to salt and moisture makes corrosion occur faster.
Engineers and other experts are working hard to improve the batteries for electric vehicles (EVs). Such progress includes corrosion protection. Here are some of the possibilities for achieving that aim.
Utilizing Specialty Coatings
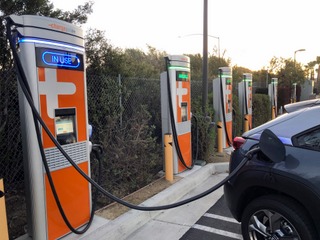
One of the challenges of EV battery design is that each one has different needs to address. However, manufacturers typically address that reality by using specialty coatings. Besides safeguarding the batteries from corrosion, these options provide fire and impact protection, plus promote better thermal management.
Keeping the batteries in the optimal temperature range is a critical part of keeping them performing properly for the expected life span. Thermal management systems for batteries are complex and often enhanced by coatings.
Electrocoating, powder coating and liquid coating are some of the methods often used for EV batteries. Some companies have investigated ways to automate these techniques, making them easier to scale. Automating the coating-application options should also bring down the overall cost of EV battery production. Then, the cars become more affordable for consumers.
Performing Lab Tests
Many corrosion protection advancements occur in laboratories before making impacts in the real world. For example, construction sites that need mechanically stabilized earth (MSE) backfill must measure the corrosivity of the surrounding soil. The soil’s resistivity indicates how easily electrical current can flow through it. The corrosion rate is lower in soil with higher resistivity.
The automotive industry commonly uses a process called cyclic corrosion testing (CCT) to see how well the various parts used in cars will resist degradation. Sometimes, CCT involves immersing the materials in water. In other cases, the components go into special chambers to get sprayed with materials. This process is often complex, especially when manufacturers want to expose pieces to various compounds.
A corrosion-related aim during these tests is to see whether water can enter various parts of a battery or other EV components. Automotive components typically have ingress protection (IP) ratings of IP67 or better. This indicates they’ll remain watertight against 30 minutes of exposure in 1 meter of fluid.
Adding an Effective Sealant
People generally think of EVs as sustainable vehicles. Broadly speaking, they are. However, there’s work to do to decrease the environmental impacts of the batteries. Some companies are exploring how to make them easier to disassemble and recycle. That’s meaningful, but batteries will also become more sustainable when they include technologies that protect them from the elements.
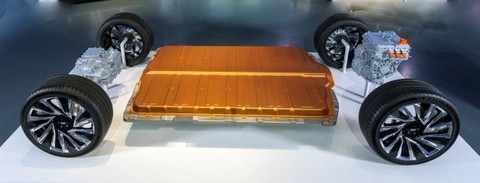
One opportunity involves using a permanent and functional seal for the car’s underbody area. For example, polyurethane sealing foam on the battery casing can protect the internal components from corrosion and moisture. The foam also has a dampening effect on vibrations while resisting chemical exposure and temperature fluctuations.
Automotive manufacturers must communicate with service providers to determine what sealant solutions they offer, how much they cost and which application methods exist, among other necessities. That information will help them make informed choices.
Battery Protection Is a Necessity
Electric vehicles are like other types of cars in that corrosion exposure is a risk associated with typical use. However, when EV manufacturers and engineering teams use some of the strategies here, they’ll mitigate the threat.
More Battery Tech:
Tech: How Long Do Hybrid Batteries Last?
Tech: Users Expect More from Batteries
Interview: Batteries Are the Problem
Tech: Toyota Going Electric with Solid-State Batteries
1 thought on “Tech: Protecting EV Batteries from Corrosion”