Simulations and Real-World Testing Move EVs Forward
As the electric vehicle (EV) market continues on its upward trajectory, improving EV component longevity is critical. Vibration testing enables manufacturers to use real-world simulations to recognize shortcomings and areas for improvement. As a result, EV parts are more reliable, durable and safer for drivers, operating at optimal efficiency for much longer.
Why Vibration Testing Is Crucial for EV Component Longevity
EV and hybrid vehicle sales increased exponentially in the United States last year, with plug-in hybrid and battery electric vehicle (BEV) purchases reaching record levels. In fact, BEVs accounted for 21.2% of total new light-duty vehicle sales in the third quarter of 2024 — up from 19.1% in the second quarter.
With growing consumer interest in sustainable transportation, manufacturers must ensure EV components’ performance and life spans are up to par. When operating, EVs experience various vibrations, from road conditions to overall motor functioning, which may cause significant wear, breakdowns and potential safety risks before their time.
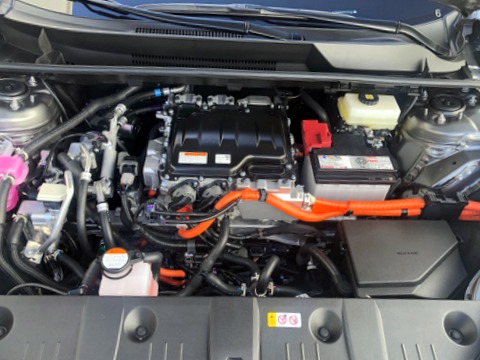
Experts use vibration testing to refine BEV suspension systems to decrease vibrations provoked by driving over rough roadways. A new design—dynamic vibration absorbing structure — has made rides more comfortable by 35% and improved road handling by 30%, ensuring a smoother driving experience on uneven terrain.
Researchers have also studied issues with electromagnetic forces in the motor—like unwanted noise, vibration and harshness (NVH)—using advanced software and vibroacoustic simulations. Analyzing these components through simulations allows them to uncover specific functions contributing to noise and vibrations at various oscillations.
Vibration testing has proven critical for various applications. For instance, advanced vibration technologies have been deployed in aerospace equipment to test their performance under extreme conditions. Experts conducted tests on the James Webb Telescope and Orion spacecraft, including acoustic test systems and laboratory shock and vibration systems on hydraulic and electrodynamic shakers.
Safety Regulations and Compliance
The National Highway Traffic Safety Administration proposed the Federal Motor Vehicle Safety Standard (FMVSS) No. 305a to supersede FMVSS No. 305. The updated standards will broaden safety requirements to cover light- and heavy-duty vehicles, including establishing new conditions for the Rechargeable Electrical Energy Storage System (REESS) and improving access to vehicle information for first responders. The REESS is the car’s battery and battery management system.
This new REESS criteria will require vibration testing to assess the performance of EV components and ensure their reliability in everyday circumstances. The proposal highlights the importance of robust testing efforts to examine diverse operational situations.
Case Study: General Motors
The automotive industry is making tremendous progress toward vehicle electrification. Naturally, vibration testing has been a cornerstone of this transition.
General Motors (GM), in particular, has utilized these advanced tests to minimize NVH in its Bolt EV motor by simulating electromagnetic and structure modeling to understand its effect. In one analysis, results indicated that the winding and toque ripples in the motor negatively impacted smooth functions and performance, giving GM a starting point for improving EV parts.
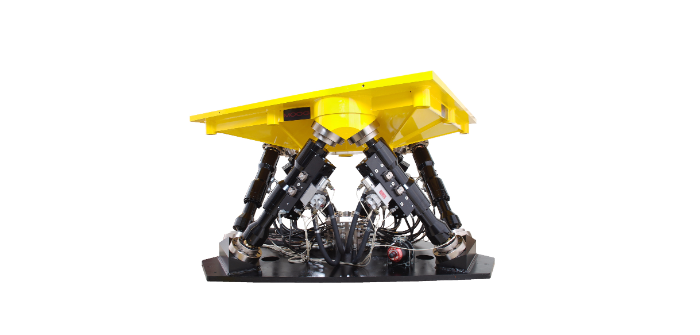
Case Study: Electric Materials Technology
Engineers need better testing tools as EV popularity intensifies. Unfortunately, current hydraulic simulation tables are incapable of achieving EV testing demands. Most vibration testing on automotive suspensions reaches 50 hertz (Hz), but EV batteries must be able to attain 150 Hz. Test labs make high-frequency simulations possible and enable battery developers to identify the charge and discharge rate in various scenarios.
For instance, in 2023, Element Materials Technology collaborated with Moog to modify and update its existing multi-axis shaker table. These refinements would enable the former to reach the higher frequency needed for EV battery testing and ensure component longevity.
A Proactive Approach to EV Component Longevity
Vibration testing is and will continue to be critical to ensuring EV component reliability and longevity. As green transportation advances, engineers must rely heavily on real-world simulations to identify potential problems early, improving vehicle performance and ensuring customer safety and satisfaction.
With electric vehicles still being a developing technology, it’s neat to learning about companies stress testing their components. I personally had to research combustion engine vehicles to find a frame design which was the least conducive to vibrations for medical reasons. Currently it’s planned to purchase an EV after a few more years or convert my current Jeep Liberty.
Garrett,
I think you’re selling EVs a little short, particularly when it comes to testing. They benefit from a century of traditional automotive technology testing experience. And EV technology is not new. There are more than two million on the road in the U.S. alone (and many millions more around the world, which in the automotive sense is very connected). If you’re concerned about ride, I’d jump into any of the current EVs and you’ll find they’re light-years ahead of your Liberty –ed.